Forged brass door handles and door hardware is generally considered to be a higher quality and more durable material than cast brass. There are several reasons for this:
Forged brass door handles’ strength and durability
Forging is a process in which metal is heated to a high temperature and then shaped into a desired shape using a combination of mechanical force and pressure. During the forging process, the metal is subjected to deformation, or shaping, which causes the atoms within the metal to become rearranged and realigned in a more uniform and dense structure. This process helps to eliminate defects and imperfections in the material, such as porosity and inclusions, and results in a material with higher tensile strength and improved mechanical properties.
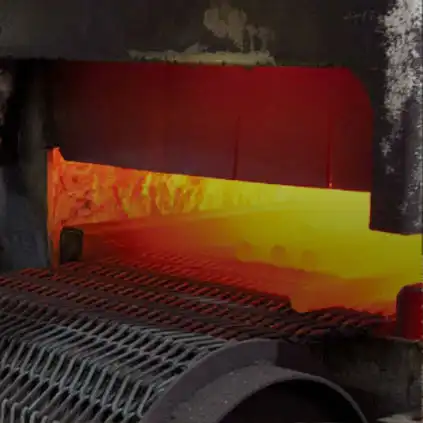
The high pressure and mechanical force applied during the forging process also help to improve the grain structure of the metal, making it more uniform and cohesive. A more uniform grain structure makes the material less prone to cracking and breaking, as the grains are more evenly distributed and better able to withstand the stresses applied to the material.
In contrast, cast brass is produced by pouring liquid metal into a mold and allowing it to solidify. This process results in a material with a less uniform grain structure and a higher likelihood of defects and imperfections. The presence of these defects can weaken the material and make it more prone to cracking and breaking under stress.
Overall, the forging process results in a stronger and more durable material compared to cast brass due to the improved tensile strength and grain structure of the material. This makes forged brass suitable for use in a wide range of applications where strength and durability are important considerations.
Forged brass door handles with higher dimensional accuracy
Forged brass parts are generally more accurate in terms of dimensions and tolerances compared to cast brass parts due to the nature of the forging process.
During the forging process, the metal is heated to a high temperature and then shaped into a desired shape using a combination of mechanical force and pressure. This process allows for a high degree of control over the shape and size of the finished product, as the metal can be shaped and molded to very precise specifications.
In contrast, the casting process involves pouring liquid metal into a mold and allowing it to solidify. The shape and size of the finished product are limited by the shape of the mold, and it is difficult to achieve precise tolerances using this process.
As a result, forged brass parts are typically more accurate in terms of dimensions and tolerances compared to cast brass parts. This is important for applications where precise dimensions and tolerances are critical, such as in the aerospace, defense, and medical industries.
In addition, the improved dimensional accuracy of forged brass parts can also result in better performance and reliability in certain applications, as the parts will fit together more accurately and be less prone to failure due to misalignment.
Forged brass door handles have better surface finish
The surface finish of a material refers to the texture and appearance of its surface, and it is an important factor to consider in many applications.
Forged brass typically has a smoother and more uniform surface finish compared to cast brass due to the nature of the forging process. During the forging process, the metal is subjected to high pressure and mechanical force, which helps to eliminate defects and imperfections in the material, such as porosity and inclusions. This results in a material with a more uniform and consistent surface finish.
In contrast, the casting process involves pouring liquid metal into a mold and allowing it to solidify. This process can result in a less uniform surface finish, as the metal may not fully fill the mold and may leave behind defects and imperfections.
The smooth and uniform surface finish of forged brass can result in a more attractive finished product, as it has a more polished and professional appearance. This can be particularly important for applications where the appearance of the product is a key consideration, such as in the jewelry or automotive industries.
In addition, the improved surface finish of forged brass can also improve the performance and reliability of the product in certain applications, as the smoother surface may be less prone to wear and corrosion.
Forged brass door handles greater design flexibility
The forging process allows for more complex shapes and designs to be produced compared to casting due to the nature of the process itself.
During the forging process, metal is heated to a high temperature and then shaped into a desired shape using a combination of mechanical force and pressure. This process allows for a wide range of shapes and designs to be produced, as the metal can be shaped and molded into almost any form. This makes it possible to produce complex and customized parts that are tailored to meet specific design requirements.
In contrast, the casting process involves pouring liquid metal into a mold and allowing it to solidify. The shape of the finished product is limited by the shape of the mold, which means that it is not possible to produce parts with complex shapes or designs using this process.
The ability to produce complex and customized shapes and designs using the forging process makes forged brass parts suitable for use in a wide range of applications, as they can be tailored to meet the specific requirements of the application. This is particularly important for industries such as aerospace, defense, and medical, where precision and customizability are critical.
In addition, the ability to produce complex shapes and designs using the forging process can also provide a competitive advantage for a company, as it allows them to offer a wider range of products and services to their customers.
Forged brass door handles have higher corrosion resistance
Corrosion resistance refers to a material’s ability to resist the degrading effects of exposure to corrosive elements, such as moisture, chemicals, and other substances.
Forged brass has a higher corrosion resistance compared to cast brass due to its more uniform grain structure and lack of defects. The forging process helps to eliminate defects and imperfections in the material, such as porosity and inclusions, which can provide openings for corrosion to occur.
In contrast, the casting process involves pouring liquid metal into a mold and allowing it to solidify, which can result in a material with a less uniform grain structure and a higher likelihood of defects and imperfections. The presence of these defects can weaken the material and make it more prone to corrosion.
The higher corrosion resistance of forged brass makes it a suitable material for use in harsh environments or for products that will be exposed to moisture or other corrosive elements. This is important for applications where corrosion resistance is critical, such as in the marine, chemical, and oil and gas industries.
In addition, the improved corrosion resistance of forged brass can also improve the performance and lifespan of the product, as it is less prone to degradation due to corrosion. This can result in cost savings for the end user, as the product will require less maintenance and replacements over time.
There are some limitations to the use of forged brass, however. It is generally more expensive to produce than cast brass due to the additional cost of the forging process and the higher level of precision required. In addition, forged brass parts are typically larger and heavier than cast brass parts due to the shaping process, which may not be suitable for certain applications.
In summary, forged brass is generally considered to be a higher quality and more durable material than cast brass due to its improved strength, dimensional accuracy, surface finish, design flexibility, and corrosion resistance. However, it is also more expensive to produce.
We have strict control over brass raw materials.
Brass is used to make Cabinet Hardware (drawer pulls, drawer handles, cabinet knobs, cabinet handles, cabinet door latches, cabinet door pulls, cabinet drawer handles), Door Hardware (door knockers, door handles, door hinges, door multi-point locks, door pulls)
Having established good relationships with local raw material manufacturers who supply a stable source of high-quality materials can be beneficial for a company in several ways.
Firstly, it can help to ensure a consistent supply of materials, which is important for maintaining production levels and meeting customer demand.
Having a dedicated person assigned to oversee the production of materials specifically for the company can also help to ensure that the materials meet the required standards and specifications.
In addition, building good relationships with raw material suppliers can lead to more favorable terms, such as bulk discounts or flexible payment terms, which can help to reduce costs and improve our business profitability.